Bowl Mill Grinding Roller Tires & Table Liners
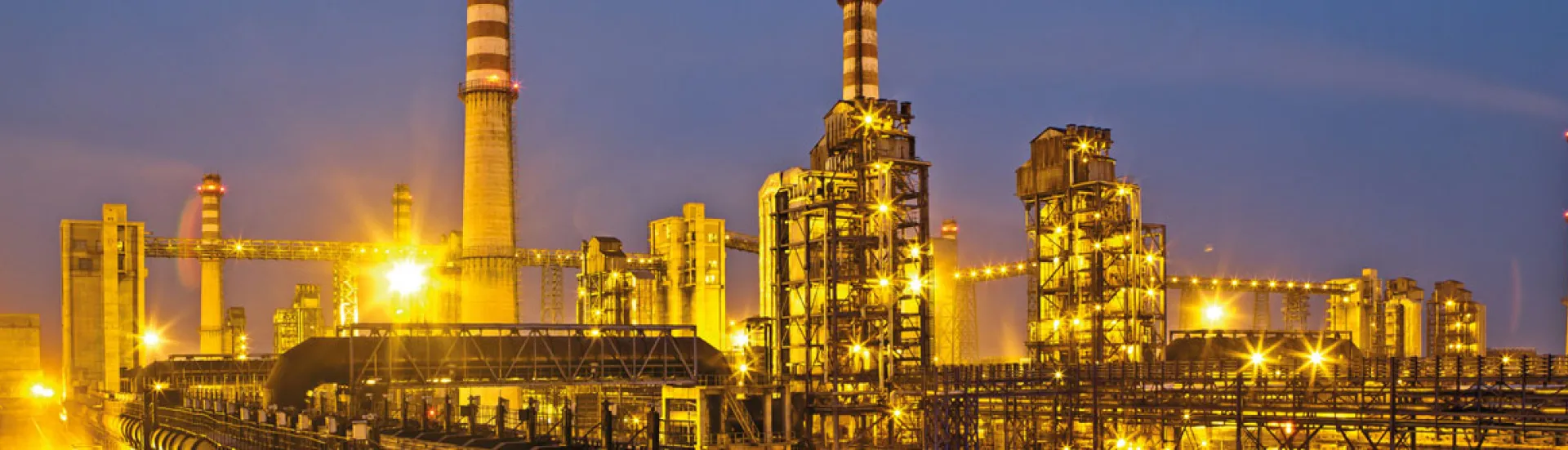
Overview
Grinding Rolls/Rollers/Tyres have evolved over the past many years. However, they have not been able to keep up with the developments in the product, and failed to give advantage to the customer in terms of higher productivity, and cost per running hour.
PRESENT SOLUTION:
- Weld Overlay Rolls
- Hi-Cr Rolls / Ceramic Embedded
IMCO makes Grinding roller tires of mill XRP 1003 modified with Zuper replaceable segments fused with Zuper metal matrix ceramic Composites as per 3D drawing attached with complete machining and finishing.
Details of parts:
1.Mother Core :
Mother core made of base material Cast Iron duly normalized and machined to undertake the necessary grooving for fitment having 450-550 MPA. Tensile strength and 250- 300 MPA. Yield strength along with Specialized hardfacing with chromium carbide (FCW) having hardness of 56-60 Hrc thickness 6-8 mm.
2. Zuper Replaceable segments fused and impregnated with Metal matrix ceramic composites:
Specialized metal matrix ceramic composites duly fused and impregnated in a sintered chromium carbides having 60-62 Hrc hardness on surface with primary and secondary carbide hardness is 790 -1500 hv and metal matrix ceramic composite hardness is upto 10-14 Gpa Vicker’s hardness.
3. Zuper METAL MATRIX CARBIDE COMPOSITE
ZUPER Metal Matrix Ceramic Composites are extremely strong abrasion resistant carbides metallurgically bonded to replaceable segments. These carbides have a minimum hardness of 770 Hv and contain carbides upto 1500 Hv most commonly used in Clinker /Limestone/ Petcoke/ Coal Plants globally.
These extremely level replicable carbides are very easy to use and can be replaced in a very short period of time. Zuper MMCC Rollers are the most cost effective VRM and Coal Mill grinding rollers in the whole world.
Our planted innovations in the metallurgy segmented make these rollers more resistant to wear as compared to traditional rollers.
4. Top plate clamp :
Top plate clamp made of base material hardened steel with hardfacing of sintered carbides having hardness of 56-60 Hrc thickness 6-8 mm fitted with high tensile bolts , suitable locking washers and locking
Features
Properties Of Zuper MMCC Segments:
Properties | Measurement |
Density of Cermets | 3.5 – 4.5 g/cc. |
Ceramic Hardness: | 10 – 15 GPA Vickers hardness |
Primary & Secondary Carbide Hardness | 770- 1500 Hv |
Max working Temperature | 700 ° C |
Know the Benefits
- Most cost effective solution
- Reduced Power utilization
- Most advanced Metal Matrix Carbide Composites
- Maximum Wear & Abrasion Resistance
- Can be easily retrofitted to any conventional Grinding Roll.
- Reduced weight of grinding roller tire up to 10%
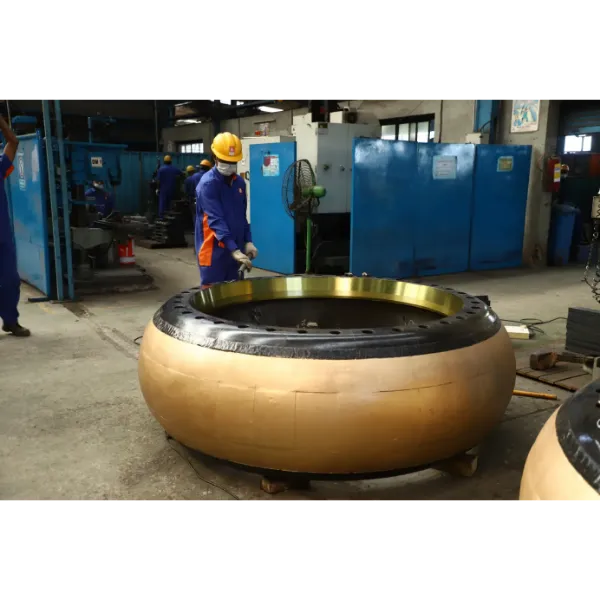
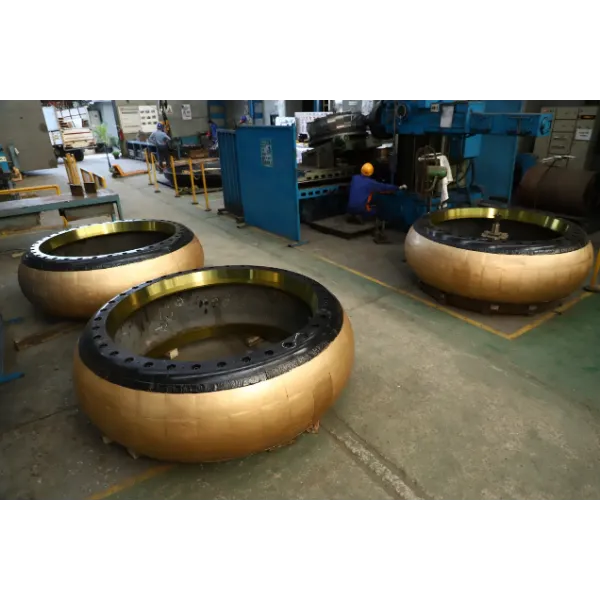
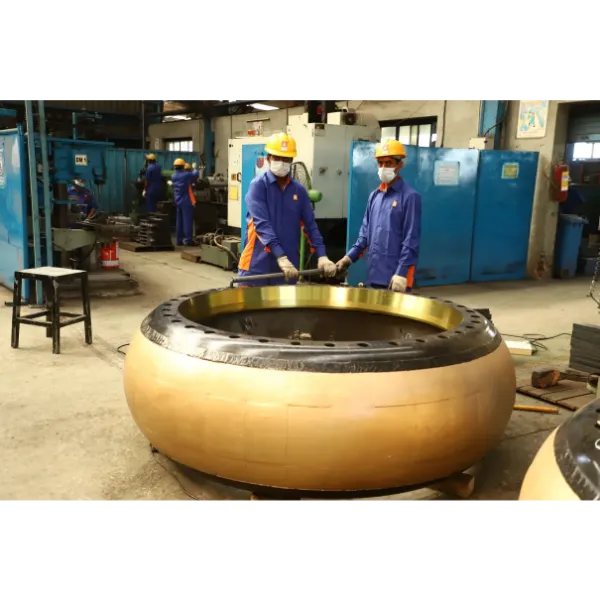
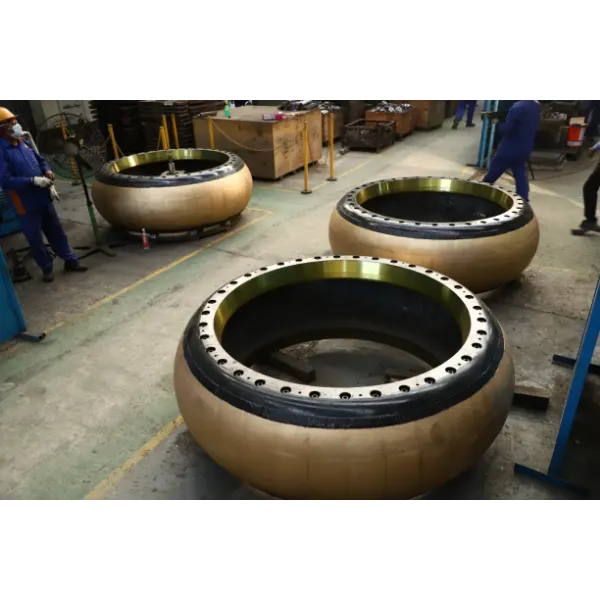
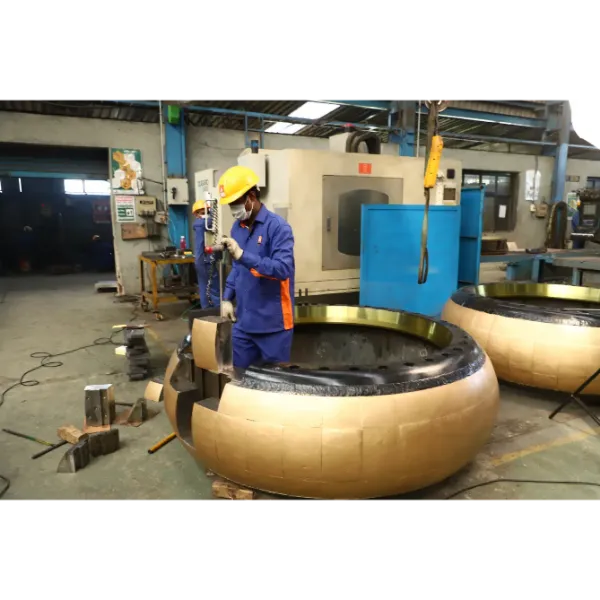
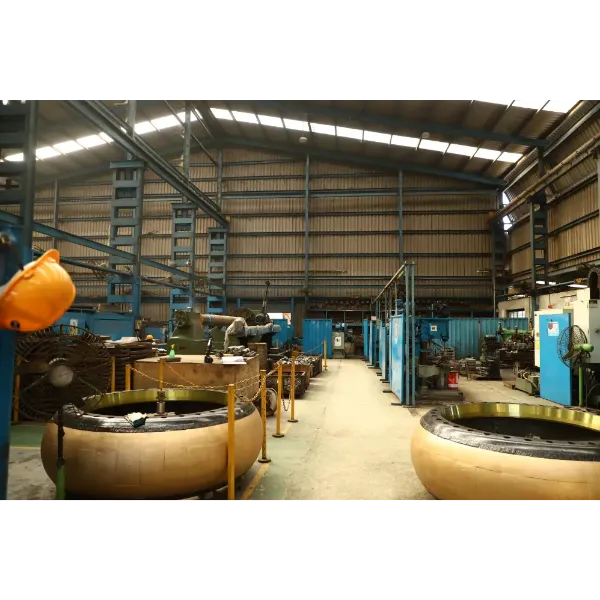
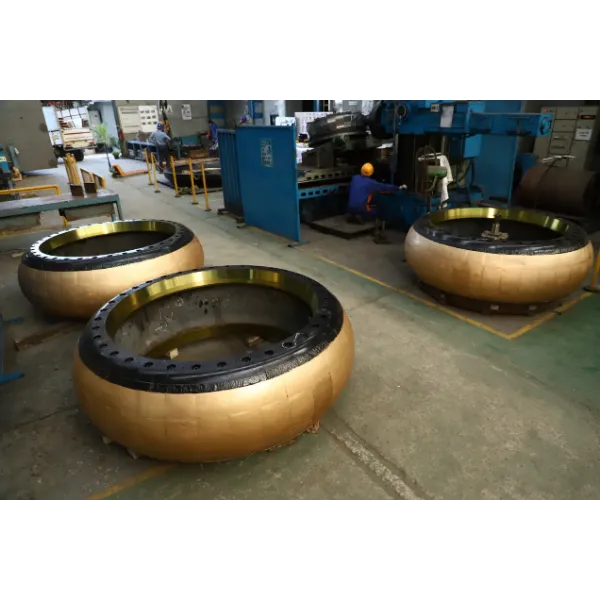
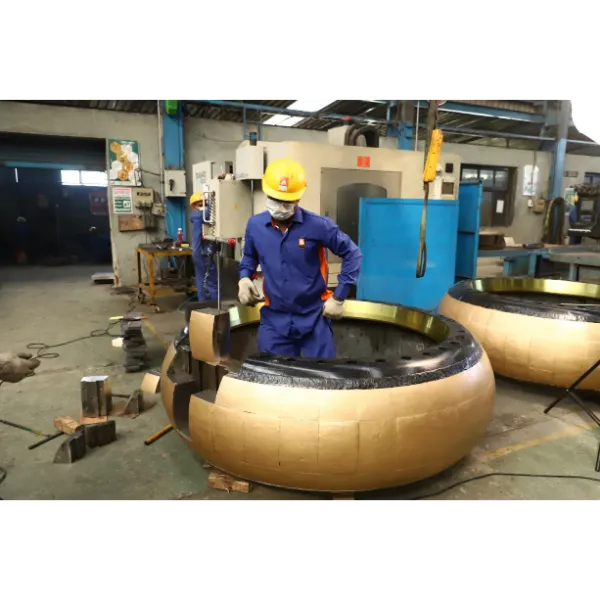
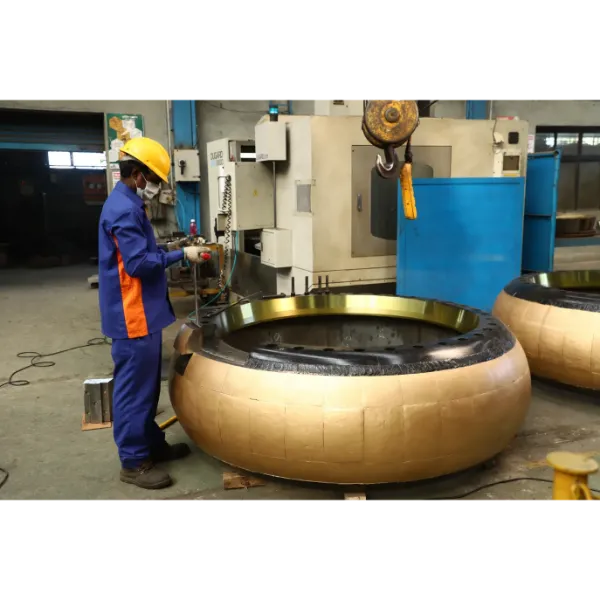
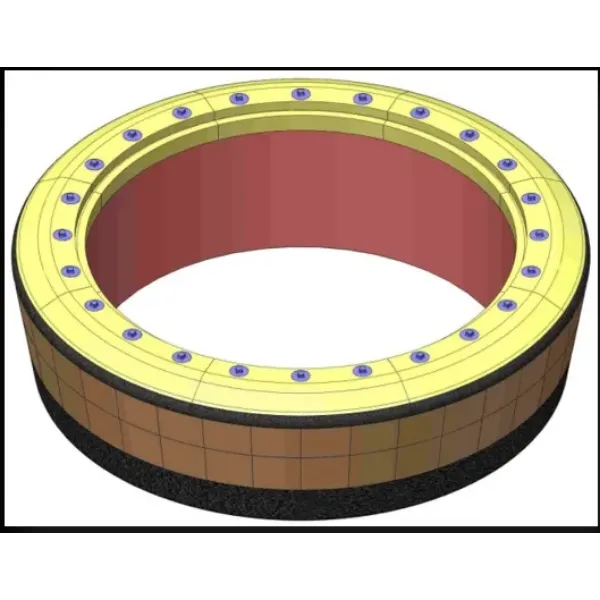
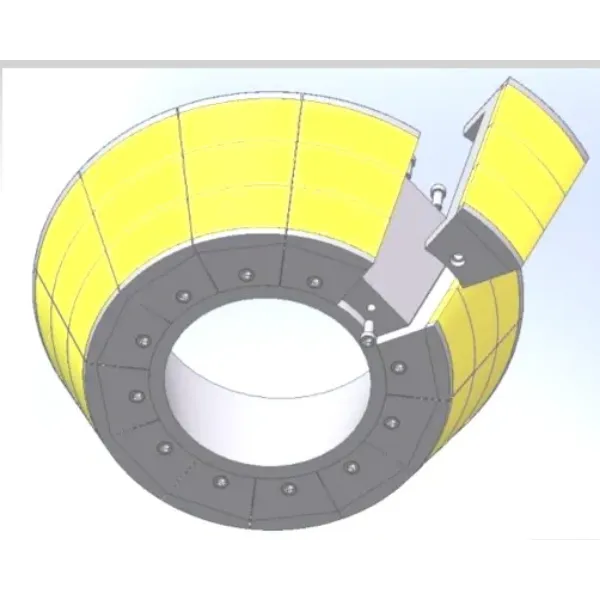
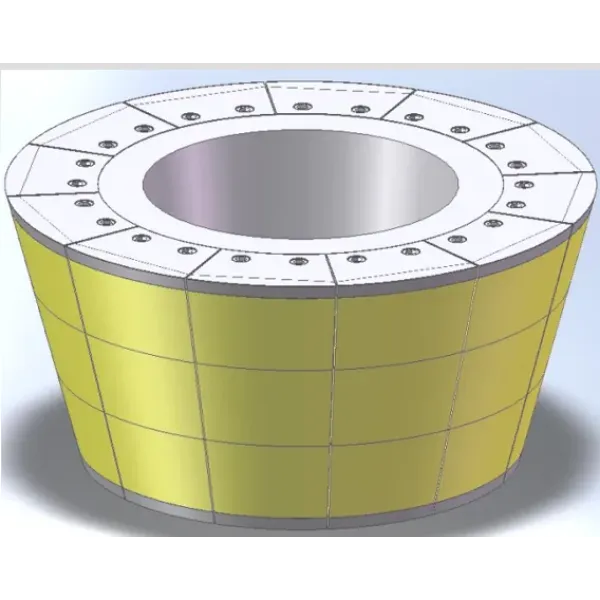
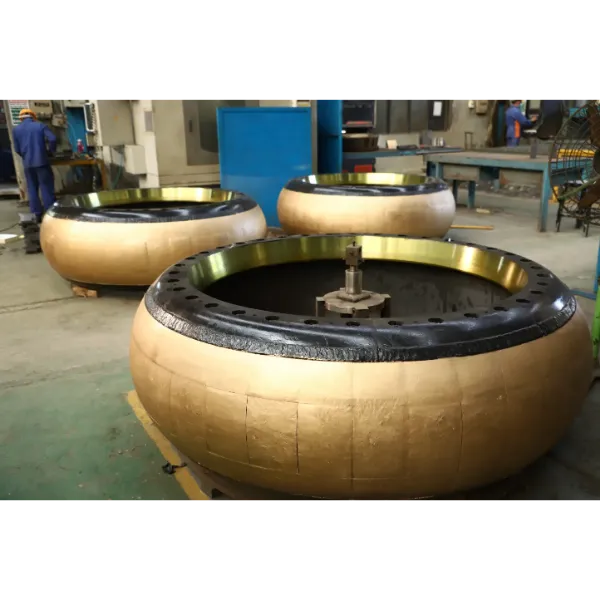
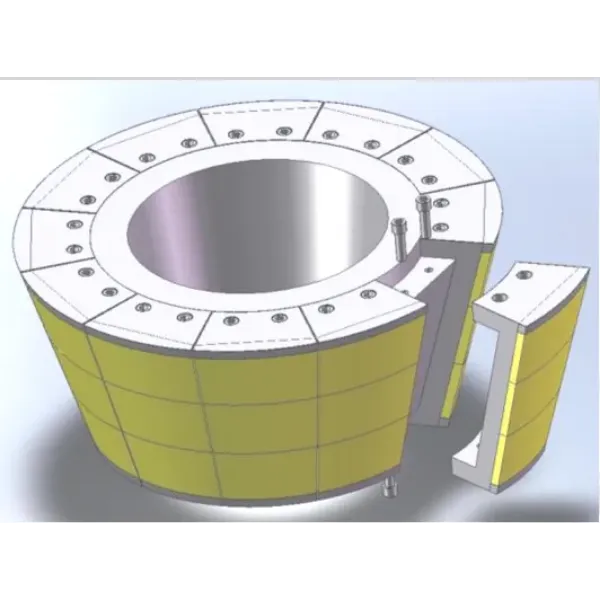
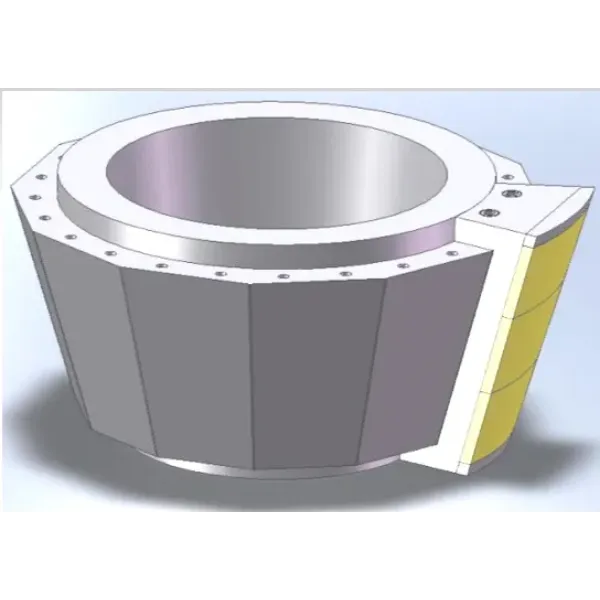
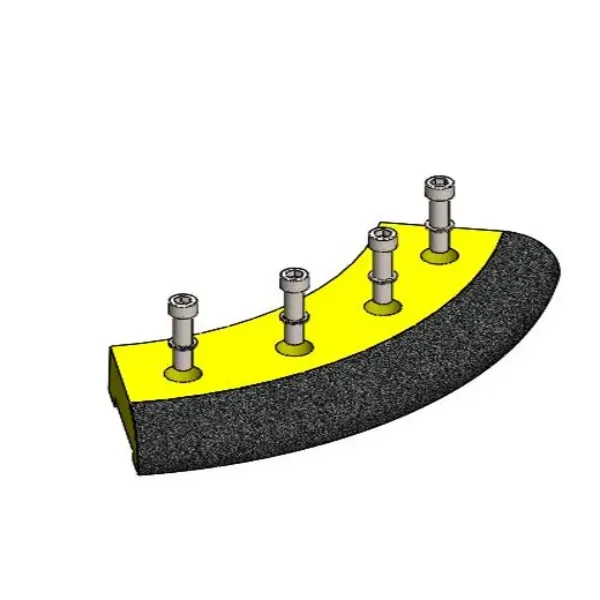