Dam Rings
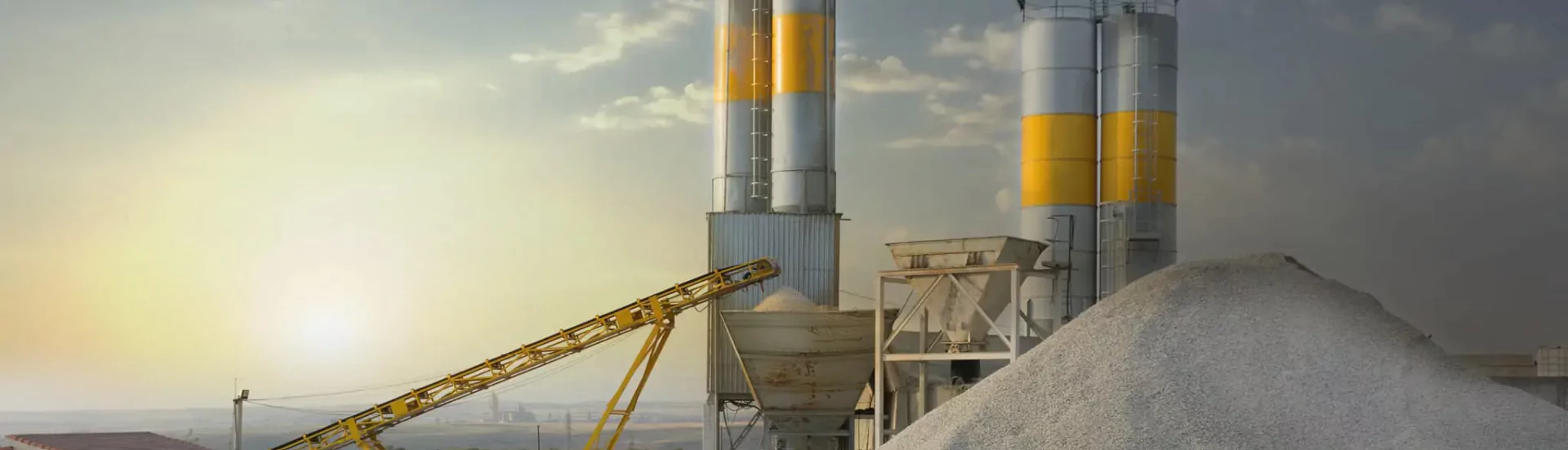
Overview
Result of Support/Dam Ring:
- Power Consumption- 1.5 kwh/ton
- Return of Investment- Less than 6 Months
- Optimization still in process
Features :
- Extremely high abrasion and erosion wear resistance offered by Zuper Metal matrix composite carbides block segmental design.
- Consistent Hardness & Micro-structure across thickness results in consistent & unmatched wear rates
- Process ensures extremely low residual stresses
- Packed & Uniform Distribution of superior Hexagonal primary carbides improving wear resistance
- Gap between support ring and grinding rolls can be maintained by providing higher thickness of Zuper metal matrix composite carbides layer.
- Highly cost effective solution.
- Hardness : 58-62 Hrc
- Reduces downtime losses.
Saving Head | Existing Solutions | IMCO solution | Remarks |
Replacement time per mill | 5-6 days | 1 day (Max) | Shut down time reduced by 80%
|
Resources required | Crane required | Only simple tools required | Imco Zuper block segments held by nuts and bolt arrangements. Only simple tools required to change segments. |
Hardfacing required | IN 3-4 weeks | No hardfacing | Imco solutions does not require any hard facing having an excellent Zuper metal matrix composite carbide metallurgy to withstand very high abrasion and erosion wear. |
Man power | 2-3 person or more | 1 person (max) | Imco replaceable segments have easy assembly and disassembly mechanisms. Only one person can remove or replace the worn out segments |
Mill efficiency | Lower (Faster wear rate) | Higher (Uniform properties throughout) | Faster wear rates result in frequent hardfacing which causes higher stresses induced in base material and frequent shutdown periods. In case of IMCO solution, having a lower rate of wear which indirectly increases efficiency and lowers the power consumption considerably. |
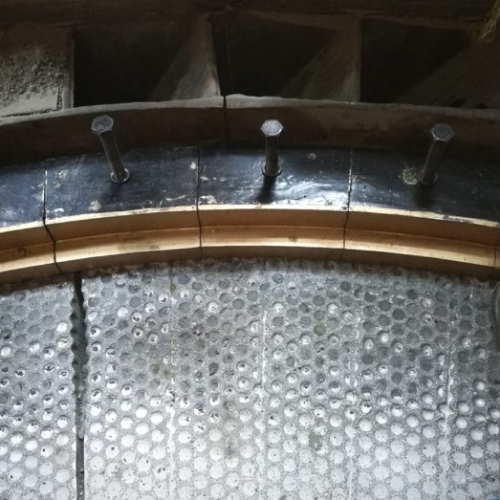
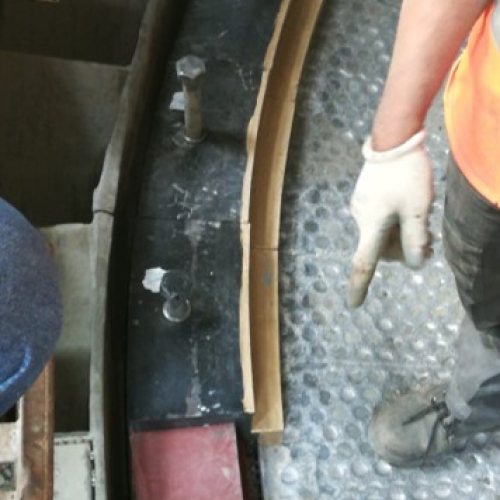
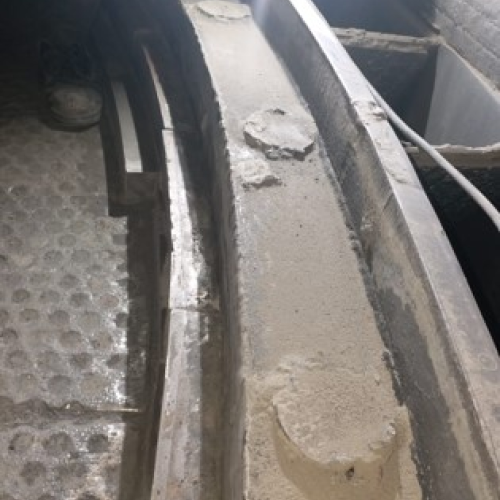
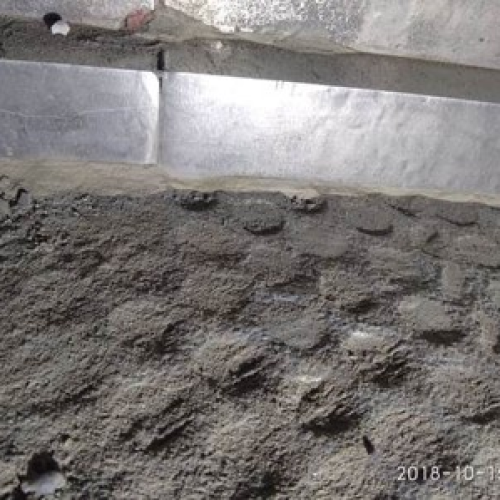