Welding Solutions
With Decades of first-hand experience in development and working in close collaboration with leading Sugar factories, we’ve developed a unique product portfolio for the Sugar industry. For metallurgically demanding welds like in the case of creating our patented Zuper Teardrops on Rollers, our specialized products have proven quality, excellent welding characteristics and are valued by welders all over the world.
Welding consumables of IMCO Alloys are used in numerous demanding areas of the Sugar Manufacturing industry, e.g., in Roller Arcing, Pinion Welding, Roller Journals, and multiple Hardfacing applications. Our new generation of flux cored wires has already been successfully applied by notable branch leaders and enables the highest process reliability.
IMCO Alloys welding has developed these high performance welding alloys working closely with leading Sugar Manufacturers worldwide. We offer a wide product range which meets the strictest safety requirements while also ensuring assurance of the highest metallurgical standards, consistently high product quality, excellent welding characteristics & excellent mechanical properties. We also inspect and refurnish used parts. Along with this we provide field support for installation & wear monitoring. Our wear expertise and comprehensive production capabilities enable our diverse customer base to improve their productivity, profitability and quality and competitiveness.
Talk to us about your wear problems, we are interested in offering cost effective modifications of standard materials for specific applications and will be pleased to be your partner in the development of new products.
For High Demanding Applications
ROLLER ARCING WIRE – ZUPER W 6800 OA
Welding consumables of IMCO Welding are used in numerous demanding areas of the Sugar Manufacturing industry. Our new generation of tubular flux cored wires has already been successfully applied by notable branch leaders and enables the highest process reliability. Zuper W 6800 OA delivers a high percentage of Chromium Carbides enabling high density per square inch and protects the lateral side of the Sugar Mill Roll against severe abrasion.
Tear Drop Electrode – Zuper R Ztd ( Zuper Tear Drop Technology)
Top quality welding consumables made by IMCO are available for the Sugar Industry. Decades of first-hand experience in development of our patented Zuper Tear Drop technology has helped us develop a specialized wire that provides users with assurance of the highest metallurgical standards, consistently high product quality and excellent welding characteristics. The Zuper R ZTD has reliable resistance to corrosion and ensures superior gripping of cane that leads to higher extraction.
Roller Arcing Rod – Zuper R 0
The Zuper R 08 is designed to uniformly spray extra hard globules on cast iron roller mills of sugar and alcohol mills. The dense spray protection coating on the sides helps reduce abrasive wear caused by bagasse drag. Welding consumables made by IMCO Alloys are trusted worldwide and have made their mark in Sugar industry applications.
Roller Journal – Zuper R 803
For metallurgically demanding structures like rollers, the proven quality of IMCO make Zuper R 803 is key to reducing costs and ensuring structural safety. The excellent welding characteristics are valued by welders all over the world.
Pinion – Zuper R 20b ( Rod), Zuper W 503 Oa (Wire)
The demands for higher efficiency with improved performance are met with the Zuper R 20B stick electrode and the Zuper W 503 OA wire. These products offer excellent resistance to sliding, rolling and friction. IMCO Alloys Welding has developed these friction, impact and abrasion resistant welding alloys by working closely with leading Sugar manufacturers worldwide.
TRPF – W 530 OaZuper
A self-shielded high carbon high chromium flux cored wire designed especially for extreme gouging type abrasive wear conditions. The weld deposit is primarily used for hardfacing of components subjected to extreme abrasion / erosion under moderate / heavy impact loads.
Hammer Body, Knife Body, Scraper & Thrash Plate – Zuper R 650
For Hardfacing applications on Hammer bodies, Knife bodies, scraper plate, etc IMCO Alloys offers this high-quality, specialized welding consumable, optimally suited for Fe, Cr and Mn based alloys. Our wide product range which meets the strictest safety requirements also ensures excellent mechanical properties.
ZUPER MAC 1250
Powersource for SAW / MIG / HARDFACING / CAG / MMAW
- 10 functional job memories to store parameters.
- Password lock of front panel.
- 2T-4T functionality for manual welding.
- Local/Remote, to operate from panel/feeder/carriage.
- Gas Test, helps to test gas flow before welding.
- Inbuilt Weld-o-meter to evaluate welding/arcing time.
- Inbuilt Protections
- OC - Over Current
- OT - Over Temperature
- OV - Over Voltage
- UV - Under Voltage
- SP - Single Phase Loss
TECHNICAL SPECIFICATION | MIG/HARD-FACING | ARC/GOUGING |
Input Supply Voltage | 330-500VAC, 3Ph | 330-500VAC, 3Ph |
Max Installed Power | 53.5 KVA/ 68.15HP | 53.5 KVA/68.15HP |
Set Voltage | 14.0 to 54.0 VDC | NA |
Current Range (Amps) | 25A-1250A | 25A-1250A |
Current@60%Duty | 1250 Amps | 1250 Amps |
Current@100%Duty | 1000 Amps | 1000 Amps |
Maximum OCV | 95 VDC | 95 VDC |
Dimension (W x L x H) mm | 460 x 1100 x 1170 | 460 x 1100 x 1170 |
Weight (KG) | 140 KG | 140 KG |
ADDITIONAL FEATURES | ADDITIONAL FEATURES | ADDITIONAL FEATURES |
Burn Back | 0.1 TO 5.0 sec | NA |
Inductance | -8 to +8 | NA |
Preflow Gas | 0.0 to 25.0 sec | NA |
Postflow Gas | 0.0 to 25.0 sec | NA |
Hot Start | NA | 0 to 100% |
Arc Force | NA | 0 to 100% |
HFWF-WIRE FEEDER FOR HARD-FACING
|
HFWC-WATER / LIQUID CIRCULATION UNIT | |
Tank Capacity | 50 Litres |
Cooling | Forced Air |
Heat Exchange | Radiator with Copper tubing |
Dimensions (W x L x H) | 382 x 582 x 450 mm |
Weight | 42 Kg |
ACCESSORY – MIG / MAG TORCH | |
A Water Cooled Torch Model RB 610D, KZ-2, 3M, 650 AMPS, 3.2 C Tip. | |
TECHNICAL DATA | |
Rating | 500 A without Gas 650 A CO2 100% Duty Cycle |
Wire Sizes | 1.6 – 3.2 |
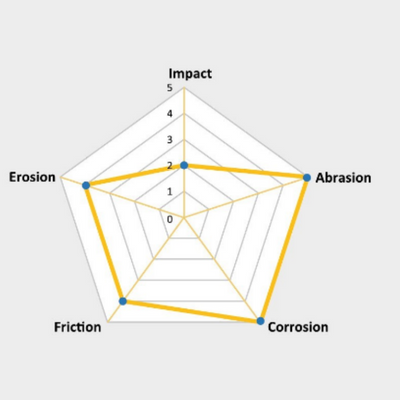
Zuper W 6800 OA is a specially developed tubular flux cored wire used for superior Arcing on nodular and grey cast iron sugar mill crusher rolls, improving the gripping efficiency and increasing the feeding rates of the sugar cane.
Zuper W 6800 OA gives great adherence of Cr-C (Chromium Carbide) drops of high density per square inch enabling much higher fiber drag and traction of bagasse, protecting the lateral side of the Sugar Mill roll against severe abrasion delivering effective yield and juice efficiency.
USP OF ZUPER W 6800 OA
• High weldability performance and ease of operation.
• High yield deposition – above 94%
• Deposit with low slag formation
• Specially developed flux cored wire for superior arcing on all types of CI rolls.
• Deposits are hard abrasion resistance globule of high alloy complex carbides.
• Uniform globule formation improves gripping properties and increased feed rate
• Average hardness 62 HRC with complex Cr carbides.
Type | Ø Dia. (mm) | Voltage (V) | Current (A) CC + | Stick-Out (mm) | Kg/h |
High Glob | 2.4 | 30 – 33 | 200 – 240 | 35 – 40 | 12.0 – 15.0 |
High Glob | 2.8 | 31 – 33 | 220 – 260 | 37 – 40 | 15.0 – 28.0 |
High Glob | 3.2 | 31 – 34 | 240 – 270 | 37 – 40 | 15.0 – 28.0 |
ZUPER R ZTD
CHARACTERISTICS
Zuper R ZTD is a special electrode designed for tear drop applications on sugar mill rolls, with superior abrasion performance, these easy and fast to execute tear drops deliver increased life without detaching or breakage even at the highest milling speeds and soil contamination.
It is designed for controlled fluidity with good arc force resulting in well fused deposits as per the desired shape over the base metal. Its metallurgical structure is based on 45% Chromium Carbides and withstand high abrasion and corrosion at high roller speeds of up to 8-10 rpm
Strong and quick arc control with easy arc striking and restriking resulting in the adequate tear drop shape and productivity while welding. Controlled fluidity and fast cooling results in uniform tera drop patterns.The best performance is achieved using negative current without overheating up to 230A in DC-ve.
TECHNICAL DATA
Hardness 1 – 2 Layer (Cast Iron) – 60 – 64 HRc
APPLICATIONS
• It is specially designed for teardrop welding on sugar mill rolls.
• Can withstand high soil contamination and speeds up to 8/10rpm.
BASE METAL
Gray or Nodular cast iron.
Type Arc Transfer | Ø (mm) | Current (A) CC -/+ | Kg/h (*) Reference |
Spray | 3.25 | 150 – 230 | 1.7 – 2.4 |
Best performance is with DC -ve polarity |
Ø (mm) | Packaging Type | Weight |
3.25 mm | Cartoon Box | 5 kg |
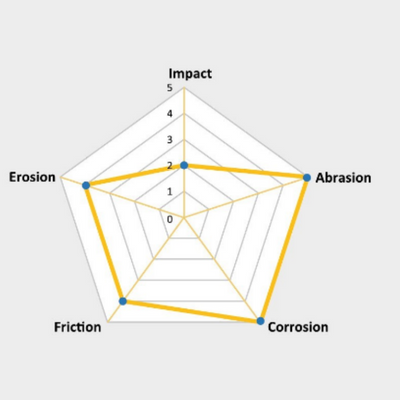
CHARACTERISTICS
Zuper R 08 is a coated stick electrode hardfacing alloy that produces a high volume fraction of wear resistant Chromium Carbides.
Zuper R 08 is designed to uniformly spray extra hard drops in Cast Irons Roller Mill for Sugar and Alcohol mill processed. This dense spray protection coating on the sides of the roller grooves reduces the abrasive wear caused by bagasse drag along the mill mechanism. The drops induce high mill productivity due to bagasse drag giving an elevated yield resulting in better juice extraction.
ZUPER R 08 : WELDING CHARACTERISTICS
High weldability performance
Easy deposition and weldability due to specific coating design
Deposit with low slag formation
WELD METAL BASE
Carbon Steel, Manganese Steel Alloyed, cast Iron, Hard Steel, stainless Steel
TECHNICAL DATA
Hardness 2 Layers (A-36) – 58 – 62 Hrc
APPLICATIONS
• Sugar Mill roller arcing / roughening
Transfer Type | Ø (mm) | Amperage (A) CC + | Kg/h (*) Depends on oscillation and dillution |
“Drop Arc” – Fine Sections | 3.25 x 350 | Low 90 – 110 | 1.3 – 1.8 |
“Drop Arc” – Thicker Sections | 3.25 x 350 | High 100 – 140 | 1.7 – 2.4 |
“Drop Arc” – Fine Sections | 4.00 x 450 | Low 140 – 190 | 2.4 – 3.0 |
“Drop Arc” – Thicker Sections | 4.00 x 450 | High 160 – 220 | 2.7 – 3.2 |
“Drop Arc” – Thicker Sections | 5.00 x 450 | High 150 – 230 | 2.9 – 3.5 |
Ø (mm) | Package Type | Net Weight |
3.25 | Metallic Cans / Carton | 15 Kg |
Others | Metallic Cans / Carton | 20 Kg |
ZUPER R 803
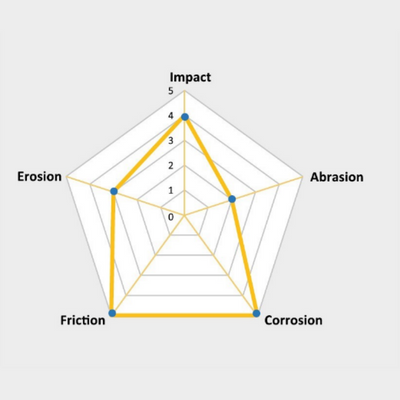
CHARACTERISTICS
A medium heavy coated, rutile type AC/DC electrode designed for the welding of low carbon 18% Cr / 10% Ni, type 304L, 304 austenitic stainless steel. Operability is excellent with a low spatter arc, producing a smooth weld bead surface and self-releasing slag. The electrode deposits X- ray quality weld metal.
REDRYING : 250°C/2 hrs. max 5 cycles, 10 hr. total.
TYPICAL APPLICATIONS
• For welding ASTM / ASME 304, 304L, 304LN, Cast CF3, CF8, food brewery and chemical process vessels, pipelines and nuclear engineering. Type 301, 302 and 303.
• Also suitable for welding type 321 stabilized stainless steel, petrochemical, power and pharmaceutical industries, paper processing plant.
WELD METAL ANALYSIS (RANGE) %
C | Mn | Si | Cr | Ni | Cu | Mo | S | P |
0.04 max | 0.5 – 2.5 | 0.35 – 0.90 | 18 – 21 | 9 – 11 | 0.75 max | 0.75 max | 0.03 max | 0.04 max |
MECHANICAL PROPERTIES (RANGE)
UTS (MPa) |
YS (MPa) | Elongation (%) (L=4D) | CVN impact strength | |
Temp | Joules | |||
520 min | 380 – 500 | 35 – 45 | 0° C | 60 – 100 |
RECOMMENDED CURRENT AND PACKING DATA
Size (mm) | AMPS AC (70V) / DC (+) | Packing / Box (Pcs) | Weight / 1000 Pcs (Kgs) |
2.50 | 60 – 85 | 95 x 5 = 475 | 20.00 |
3.15 / 3.20 | 80 – 100 | 60 x 5 = 300 | 32.00 |
4.00 | 110 -140 | 38 x 5 = 190 | 50.00 |
5.00 | 130 – 200 | 25 x 5 = 125 | 80.00 |
Length : 350 mm
Packing : 20 kgs per Carton
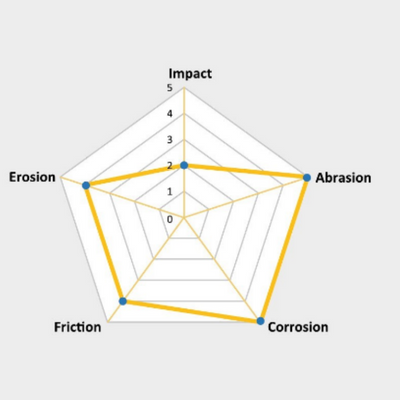
CHARACTERISTICS
A self shielded high carbon high chromium flux cored wire designed especially for extreme gouging abrasion conditions. The weld deposit is primarily used for hardfacing components subjected to extreme abrasion / erosion under moderate / heavy impact loads. The weld deposit contains a high proportion of hard primary chromium carbides in a tough martensitic – secondary carbide eutectic matrix. The weld deposit is non machinable.
TECHNICAL DATA
- Polarity : DC wire positive
- Size : 1.60 mm, 2.00 mm, 2.40 mm and 2.80 mm
- Typical weld metal chemistry has more than 25% Cr with Mn,
- C and Si as the other alloying elements besides Fe.
- Hardness (3 layers) : 58 – 62 HRC
APPLICATIONS
Worn Out Ni-Hard and high chrome crusher rolls, table liners, tyres etc. for the coal mill in thermal power station and crushing mill in cement plants. Gyratory crusher cones and mantles, catalyst pipes and bends, slurry pipes and value bodies, dredge pump bodies, extruder screws, mining & earthmoving equipment, blast furnace bells, coal pulveriser rolls, crusher hammers, shovel edges wear plates, TRPF rollers in sugar mills etc.
WELDING PARAMETERS
Size | Range |
1.6 – 2.0 mm | 200 – 350 A, 26 – 28 V |
2.4 – 2.8 mm | 250 – 400 A, 28 – 29 V |
WIRE EXTENSION (STICK OUT)
35 – 40 mm
PACKAGING
12.50 / 15 Kg spool sealed in polythene bag and shrink wrapped in a corrugated box.
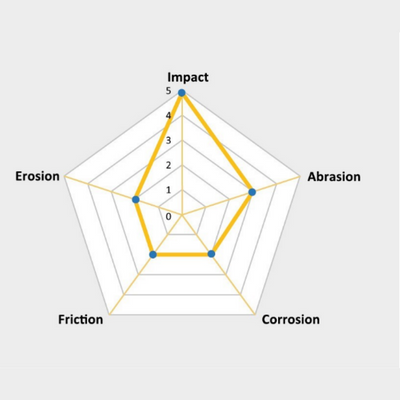
CHARACTERISTICS
An electrode for excellent resistance to Sliding and rolling Friction with Moderate Impact.
The Zuper R 20B deposit has a high strength and moderate toughness. Hence it is ideal for heavy rolling and sliding friction involving only moderate impact. The electrode, welds with a stable arc depositing a very fine and evenly rippled bead. It can be used on Mild Steel, Carbon Steel and Low Alloy Steel.
PROCEDURE
- Clean the welding area of damaged, fatigued, worn out or cracked material.
- Use the lowest possible current and short arc. Avoid excessive weaving.
APPLICATIONS
- The electrode can be used in all welding position it is ideal for field application
- The obvious fields of application include building up of worn out rolls, anvils, crushing rolls, brake shoes, forging dies, articulate track, edges of bull dog blades, sprocket wheels, pneumatic equipment, wheels flanges, chassis, idler, gear, pinion etc
- Excellent for pinion rebuilding applications in sugar, steel, cement and other industries.
WELD METAL ANALYSIS (RANGE) %
Size (mm) | Current Range (Amps) |
3.15 | 95 – 125 |
4.00 | 120 – 165 |
5.00 | 160 – 210 |
PACKAGING
20 Kgs Per Carton
Length : 450 mm, 350 mm
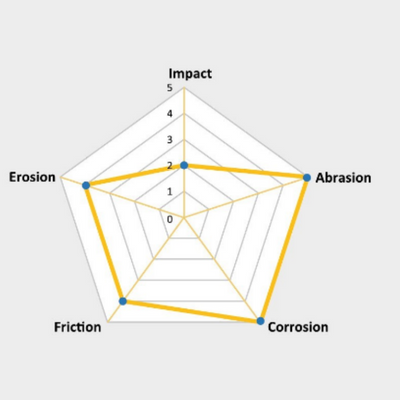
CHARACTERISTICS
A self shielded flux cored wire designed for building up applications for parts subjected to wear and impact. Good Impact properties and resistance for cold deformation. Weld deposit can be easily machined with carbide tipped tolls or flame cut.
TECHNICAL DATA
Polarity : DC wire positive
Size : 1.60 mm, 2.00 mm, 2.40 mm and 2.80 mm
Typical weld metal chemistry has Cr, Mn in the deposit besides Fe.
APPLICATIONS
A low alloy steel flux cored wire for mainly building up purpose on crane wheels, tractor, rails, steel shafts, trunions, gears, undercarriage of earthmoving equipment, excavator pins etc.
WELD METAL ANALYSIS (RANGE) %
Welding Parameter Guidelines | Size | Range |
1.6 – 2.0 mm | 200 – 350 A, 26 – 28 V | |
2.4 – 2.8 mm | 250 – 400 A, 27 – 29 V |
WIRE EXTENSION (STICK OUT)
35 – 40mm
PACKAGING
12.50 / 15 Kg spool sealed in polythene bag and shrink wrapped in a corrugated box.
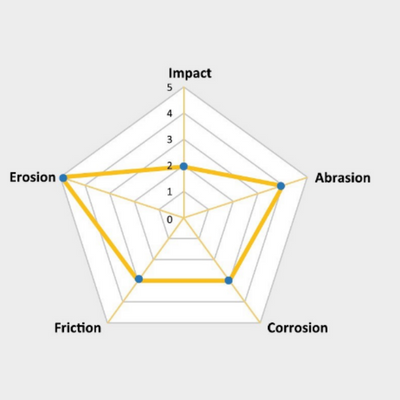
CHARACTERISTICS
Abrasion resistant wear protection.
This electrode gives an air-hardening type weld deposit which is resistant to severe abrasion and moderate impact between metal to mineral wearing stresses. It provides moderate resistance to corrosion and scaling with its alloy based on Fe, Cr and Mn.
SPECIAL FEATURES
• Smooth arc with low spatter.
• It is very easy to use in all positions. Excellent weld bead appearance.
PROCEDURE
• Clean the welding area of damaged, fatigued, worn out or cracked material.
• Use the lowest possible current and short arc. Avoid excessive weaving.
TECHNICAL DATA
Hardness : 55 – 58 HRC
APPLICATIONS
Bulldozer blades. Excavator teeth, metal cutting & forming tools, hot & cold punching dies, bucket lips, chutes, conveyors, shears & croppers, oil expellers, pulping knives. Ploughshares, road graders, crusher Hammers, caterpillar treads, cane & bamboo cutting knives, etc. Recommended for applications involving metal to mineral wear.
WELDING PARAMETERS
Size (mm) | Current Range (amp) (AC/DC+ve) |
3.15 | 90 – 120 |
4.00 | 120 – 170 |
5.00 | 160 – 240 |
PACKAGING
20 Kgs Per Carton
Length : 450 mm
ARC WELDING FUMES AND GASES
The fume plume contains solid particles from the consumables, base metal, and base metal coating. For common mild steel arc welding, depending on the amount and length of exposure to these fumes, most immediate or short term effects are temporary, and include symptoms of burning eyes and skin, dizziness, nausea, and fever. Long-term exposure to welding fumes can lead to siderosis (iron deposits in the lungs) and may affect pulmonary function. Bronchitis and some lung fibrosis have been reported.Some compounds which may be in welding fume, and reported health effects of overexposure are below. See the SDS for the consumable product used for specific information.
• Barium may cause severe stomach pain, slow pulse rate; irregular heartbeat, ringing of the ears, convulsion and muscle spasms. In extreme cases it can cause death.
• Cadmium fumes can be fatal even under brief overexposures, with symptoms much like metal fume fever.
• Chromium and its compounds are on the IARC (International Agency for Research on Cancer) and NTP (National Toxicology Program) lists as posing a cancer risk to humans. Some forms of these metals are known or suspected to cause lung cancer in processes other than welding and asthma has been reported.
• Manganese: Manganese overexposure may affect the central nervous system, resulting in poor coordination, difficulty in speaking, and tremor of arms or legs. This condition is considered irreversible.
• Nickel: Nickel and its compounds are on the IARC (International Agency for Research on Cancer) and NTP (National Toxicology Program) lists as posing a cancer risk to humans.
• Silica: Overexposure can cause severe lung damage (silicosis).
Crystalline silica is present in submerged arc flux.
• Zinc: Overexposure to zinc may cause metal fume fever with
symptoms similar to the common flu.
Your work area has adequate ventilation when there is enough ventilation and/or exhaust to control worker exposure to hazardous materials in the welding fumes and gases so the applicable limits for those materials is not exceeded. See the SDS for the legal limits, the OSHA PEL (Permissible Exposure Limit), and the recommended guideline, the ACGIH TLV (Threshold Limit Value). Confirm that if the worker exposure does not exceed the applicable exposure limit for compounds in the fumes and gases by having an industrial hygienist take and analyze a sample of the breathing air. A respirator may be required if exposure cannot be controlled to the PEL or TLV.
Read the product label and material safety data sheet for the electrode posted in the work place or in the electrode or flux container to see what fumes can be reasonably expected from use of the product and to determine if special ventilation is needed. Know what the base metal is, and determine if these is any paint, plating, or coating that could expose you to toxic fumes and/or gases. Remove it from the metal being welded, if possible.
If you start to feel uncomfortable, dizzy or nauseous, you may be overexposed to fumes and gases, or suffering from oxygen deficiency. Stop welding and get some fresh air immediately. Notify your supervisor and co-workers so the situation can be corrected and other workers can avoid the hazard. Be sure you are following these safe practices, the consumable labeling and SDS and improve the ventilation in your area. Do not continue welding until the situation has been corrected.
EDUCATION SOLUTIONS
IMCO ALLOYS WELDING TECHNOLOGY & TRAINING CENTRE
• Committed to the transfer of knowledge to anyone desiring to learn the craft and science of welding
• Welding educator train-the-trainer professional development workshops and seminars
•AWS CWI preparation training
• Welding design, alloy and other seminars for welding engineers
• Training the next generation of welders using the technology and tools demanded by manufacturers and contractors today Accredited Testing Facility onsite
Contact us at : info@imcoalloys.com
CUSTOM TRAINING
Raise The Bar on Skill Development
• Our expert instructors can design a custom results-oriented training program just for you
• Training can be conducted at your location or at our Welding Technology & Training Center in Mumbai, MH
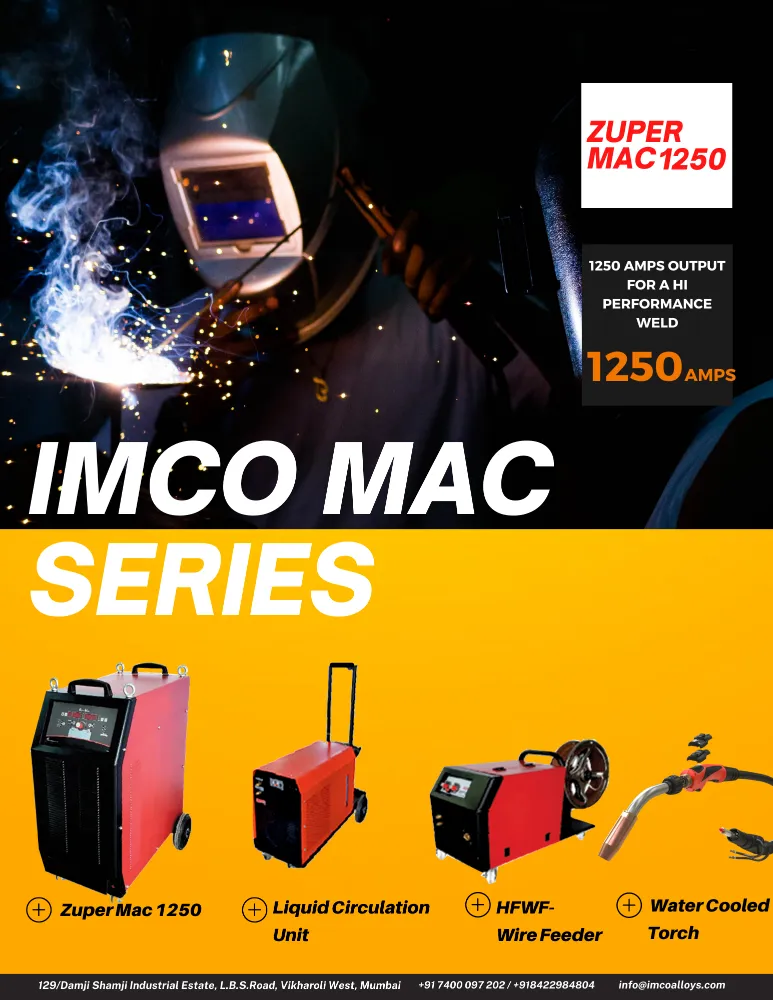
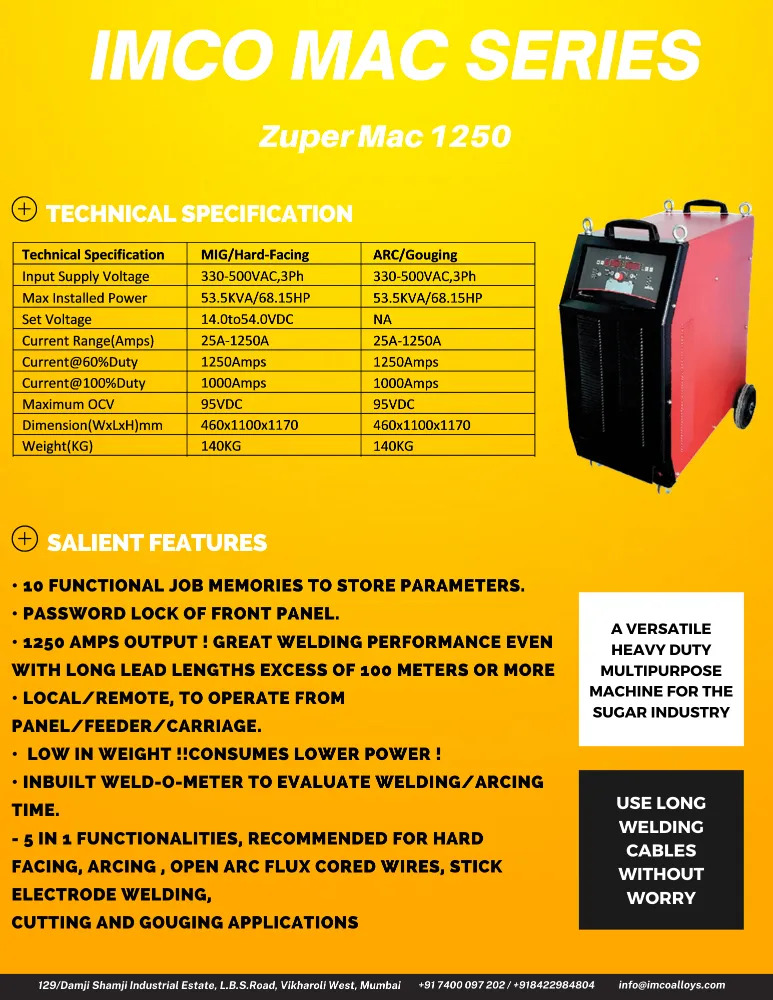
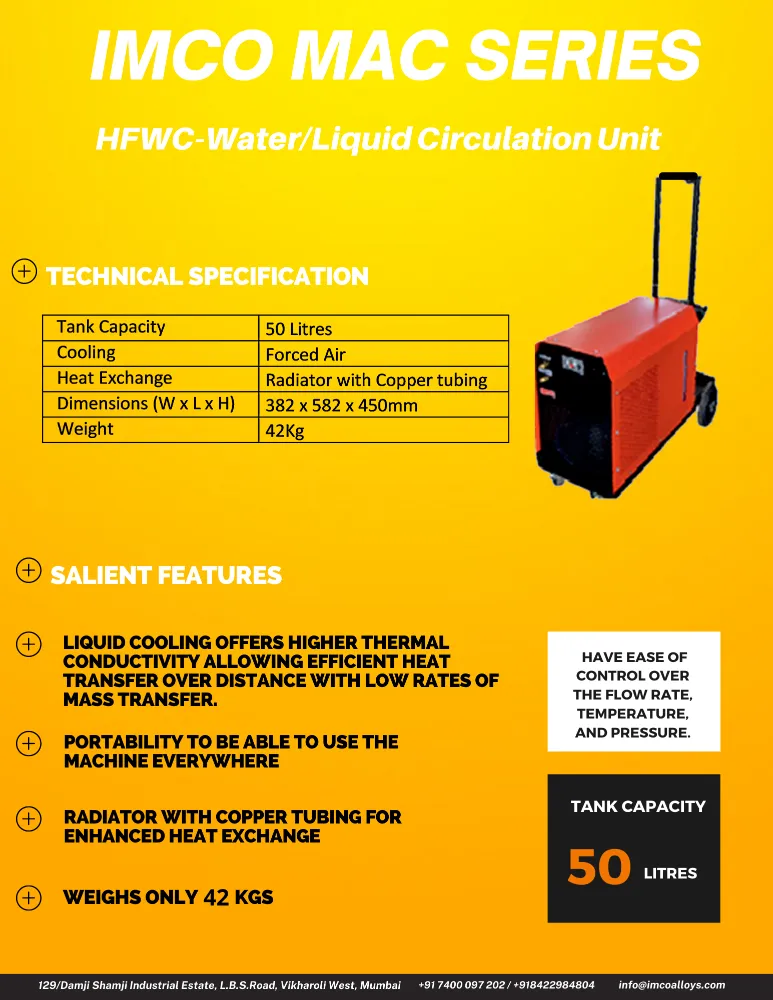
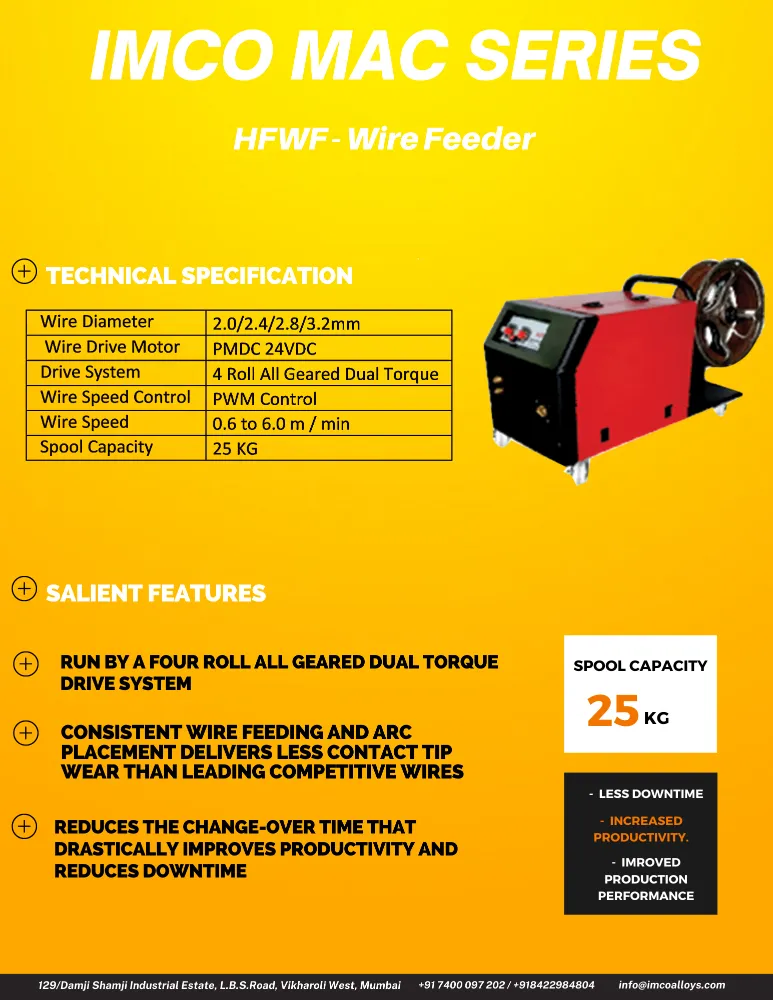
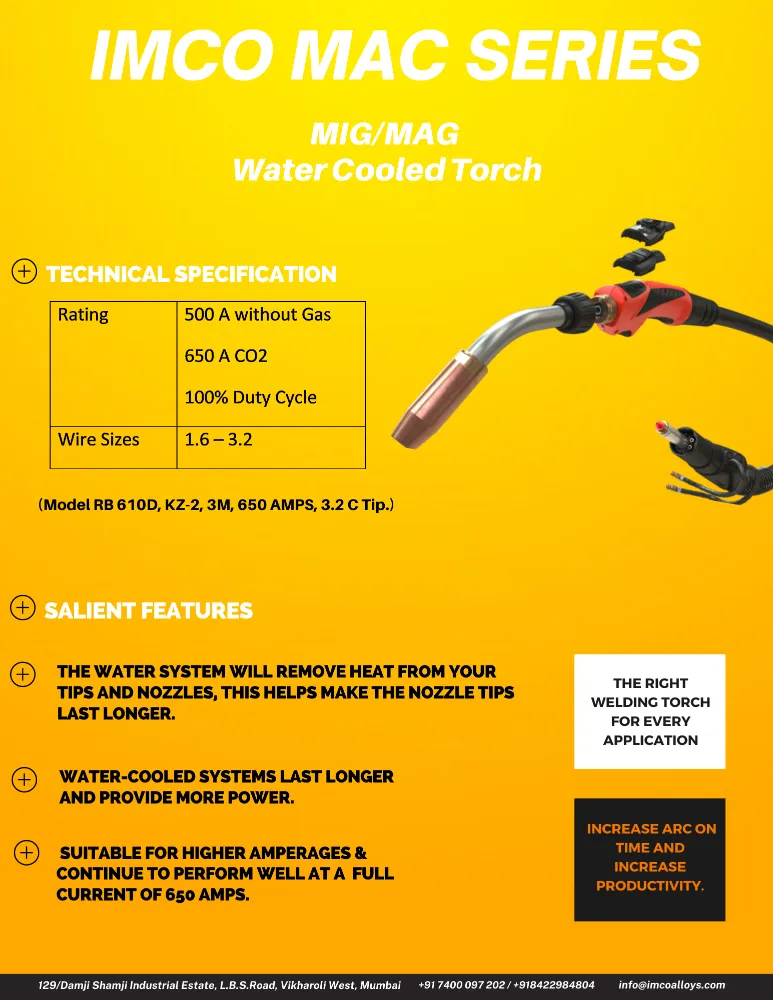